Developed and improved for over 40 years, the motorised drive rollers or MDR are the core component of advanced automated conveyor systems, it is now widely used and praised by a variety of industries and innovative logistic centers around the world.
MDR are used in the design of high capacity, cost efficient, flexible, reliable and safe installations.
Our extensive range of MDR and customisation options, can efficiently drive most types of conveyor applications, for light, medium or heavy loads transportation. It allows flawless automated material flows, all along the intralogistic processes (reception, storage, order preparation, shipping, assembly…)
The MDR are controlled either by internal circuit boards, or with external controllers, which range from standard control features (speed, direction, ...), to ZPA integrated logic, up to intelligent programmable IoT networked controllers.
Flexible and modular
- Easy integration within the conveyor
- Customised sizes
Cost efficient
- Almost maintenance free
- Extended product life
- Low power consumption
Safe
- Low voltage
- Stoppable by hand
- Quiet operation
Intelligent
- Integrated control logics (ZPA, slug, train …)
- Configurable speed, direction…
- Network communication (IoT)
- Predictive maintenance
Green
- Limited energy consumption
- Clean and recyclable
Products
Series PM 500-FE
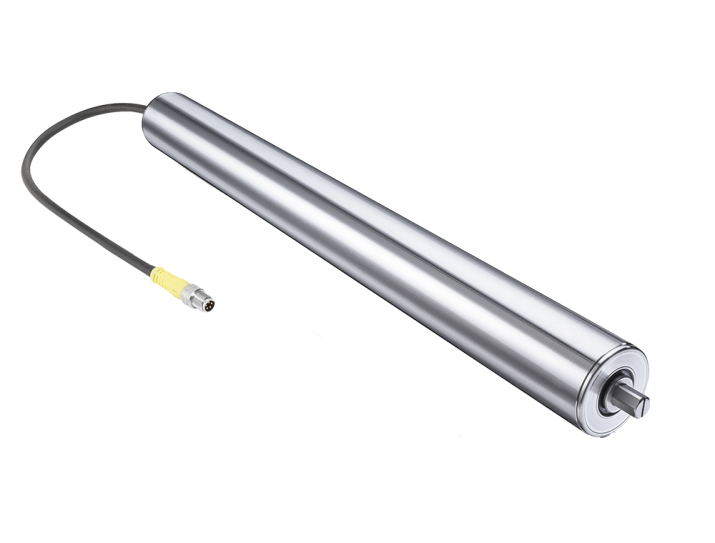
It's designed for conveying light and medium loads for order preparation, distribution an dfor assembly lines. The circuit board is separated from the gear motor in order to optimize the performance, durability of the roller and to offer diverse functions such as pulse signals, acceleration/deceleration, optional position holder. The assembly can be controlled by PLC.
ELEKTROMECANICAL
Direct current and brushless
24V DC (+/- 10 %) - ripple ratio < 10 %
Insulation index
E
Operation at 40°C
Continuous: 100%
Intermittent:
1800 starts / hour maxi
Minimum duty cycle = 1 s ON/ 1 s OFF
ED = ON / (ON + OFF) ≤ 50 %
Brakes
Dynamic braking
Protection index
IP54 (IP65 or cold room, on request)
Cable length
300 mm with JST connector - 9 pins
Protection
Thermal protection (>95°C for circuit board, >110°C for motor)
Protection against induced voltage
Environment
0°C/+40°C - no condensation - or corrosive or explosive atmosphere
Vibrations < 0,5G
Sound level
≈ 52 dB nominal 1 meter away
Speed code
15 25 55 90
Reduction ratio
1/44,90 1/26,67 1/12,64 1/7,5
Connector
9-pin JST #S9B-XH-A
CONTROL
Circuit board functions
see characteristics of CBM-105 and HB 510
Series PM 500-VE
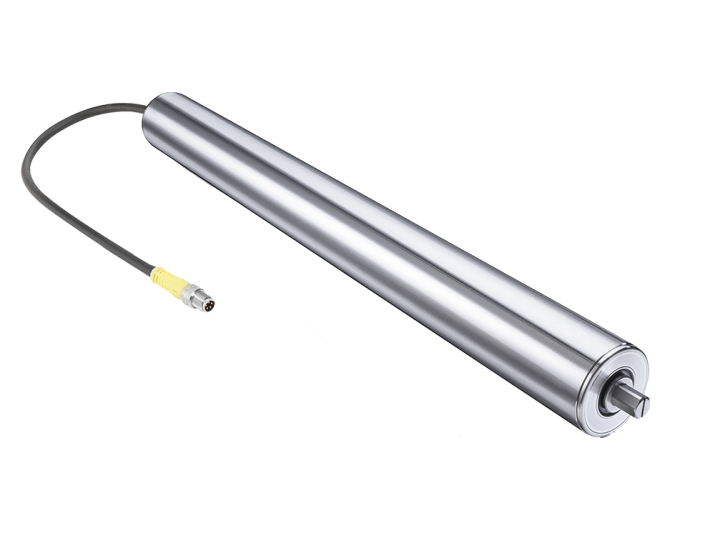
ELEKTROMECANICAL
Direct current and brushless
24 VDC (+/- 10 %) - ripple ratio < 10 %
Insulation class
E
Operation at 40°C
Intermittent: max. 1800 starts / hour maxi
Minimum duty cycle = 1 s ON / 1 s OFF
ED = ON / (ON+OFF) ≤ 50 %
Brake
Dynamic braking
Cable length and type
300 mm with M8-5P connector
Protection Index
IP54 (IP65 or cold room, on request)
Protection
Thermal protection (>95°C for circuit board, > 110°C for motor)
Protection against induced voltage
Environment
0°C/+40°C - no condensation - or corrosive or explosive atmosphere - Vibrations < 0,5 G
Sound lvel
≈ 52 dB nominal 1 meter away
Speed code
17 25 60 90
Reducion ratio
1/44,97 1/26,67 1/12,65 1/7,5
CONTROL
Circuit board functions
see characteristics of CBV-108, HBV-609 and IB-P
Series PM 500-XC

It's designed for conveying lines with light and medium loads (up to max. 300 kg) and is suitable for working environments such as those exposed to liquids and dust.
ELECTROMECANICAL
Direct current and brushless 24 VDC
24 VDC (+/- 10 %) - ripple ratio < 10 %
Insulation class
E
Operation at 40°C
Continuous: 100%
Intermittent: 1440 starts / hour maxi
Minimum duty cycle = 1s ON / 1s OFF
ED = ON / (ON + OFF) ≤ 40 %
Brakes
Servo-brake
Protection index
IP54
Cable length
500 mm with M8 connector - 5 pins snap-in type
Protection
Against overload by integrated thermistor
Against polarity reversal 0 - 24 VDC
Current limitation within circuit board
Integrated fuse 8A
Thermal protection (> 95°C for circuit board)
Protection against under supply (over 1s under 15 VDC)
Protection against induced voltage (> 40 VDC over 2s)
Protection against motor lock (> 0.5s)
Environment
0°C / + 40°C - no condensation - or corrosive or explosive atmosphere
Vibrations < 0,5 G
Sound level
≈ 54 dB nominal 1 meter away
Speed code
17 30 60 90
Reduction ratio
1/44,90 1/26,67 1/12,64 1/7,5
Start / Stop
Start: ≥ 2.0 VDC impedance ≥ 35kΩ
Stop (servo-brake): 0 ~ 1.9 VDC / Start
Speed variation
By external voltage,10 speeds, impedance ≥ 35kΩ
Error signal
NPN open collector, thermal, low voltage, back EMF.
Error signal is discharged when motor is locked condition for approx. 6s. Error signal is discharged when there is a speed deviation of +/- 20% from set speed for 10s.