- Individual components for fast solution-finding
- Available at short notice
- Economical
Products
Skate wheel conveyors
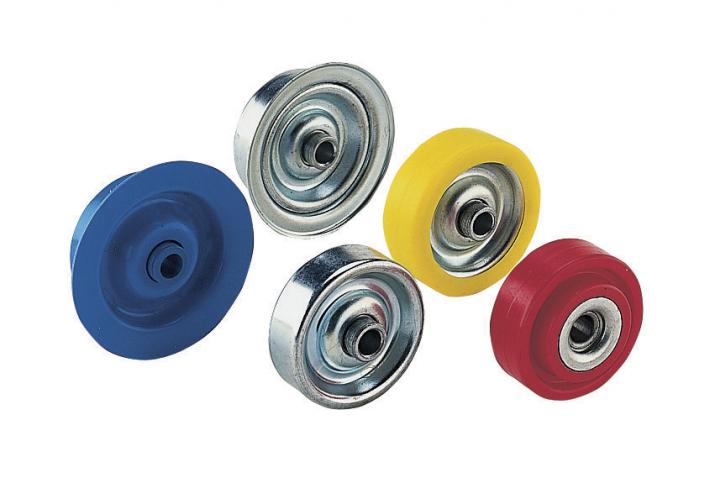
Frame structure
Steel C-profile, galvanised, with bolted cross braces
Frame dimensions: 100 x 30 x 2 mm
Min. roller spacing: 25 mm
Skate wheels
Conveyor skate wheels Ø 48 mm made of plastic or steel, ball bearing mounted, steel axle Ø 8 mm
Standard wheel spacings: 50 mm, 75 mm, 100 mm, 150 mm
Conveyor width
The width is determined by the properties and weight of the unit load – the unit load should be resting on at least 3 skate wheel axles.
Standard widths
320 mm, 470 mm, 620 mm
Standard conveyor lengths
1000 mm, 2000 mm, 3000 mm
Surface finish
Zinc plated
Ball rollers
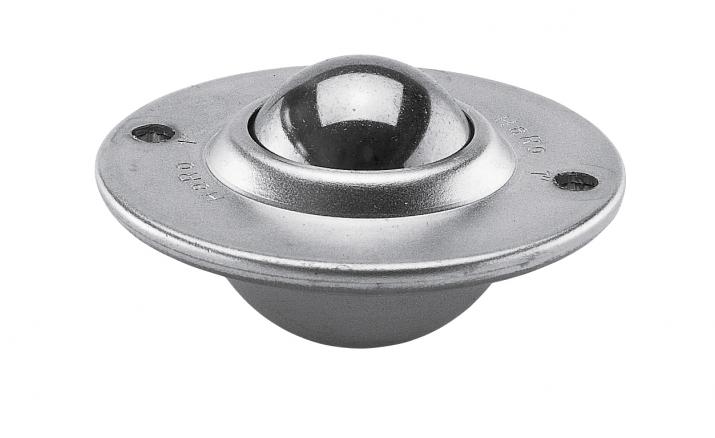
Technical execution
Housing: Solid steel or stainless steel
Balls: Bright steel, plastic or stainless steel
Felt ring seal: all ball bearing elements from size Ø 22 mm upwards are protected against soiling by a felt ring seal
Choice
Solid ball rollers: for extreme uses
or impact loads
Steel plate ball rollers: for continual loads
Stainless steel balls: for use outdoors or in damp conditions
Plastic balls: for conveyed materials with a sensitive surface
Advantages
Low friction resistance
Optimum possibilities for adaptation to the object conveyed
Ball transfer tables
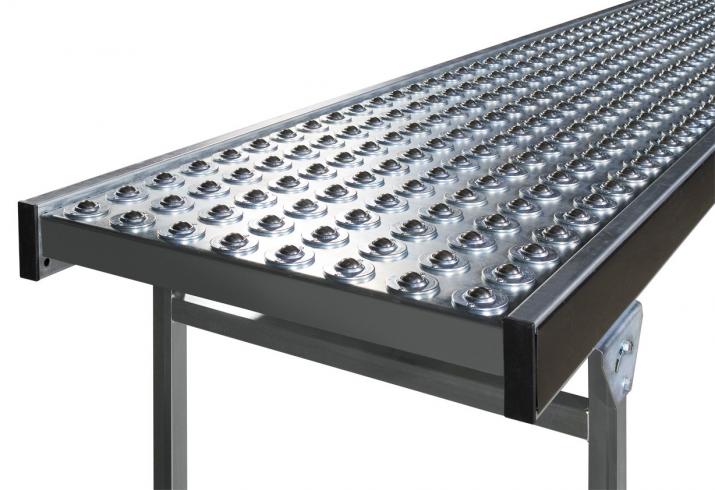
Frame structure
Steel C-profile, galvanised, with bolted cross braces
Frame dimensions: 100 x 30 x 2 mm
Min. roller spacing: 75 mm
Ball rollers
Ø 25.4 mm, type CL-8 (standard), load capacity 60 kg/roller
Conveyor width
The width is determined by the properties and weight of the unit load – the unit load should be resting on at least 3 ball rollers (3-point surface Support)
Standard widths: 470 mm, 620 mm, 770 mm
Standard conveyor lengths: 500 mm, 1000 mm, 2000 mm
All-side rollers and skate wheel rail tables
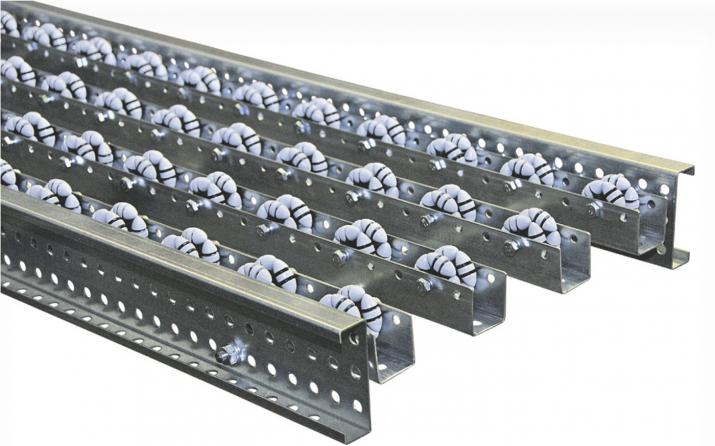
Al-side roller table
Frame structure
Steel C-profile, galvanised, with bolted cross braces
Frame dimensions: 100 mm x 30 mm x 2 mm
Conveying elements
All-side rollers type ASR50
Conveyor width
The width is determined by the properties and weight of the unit load – the unit load should be resting on at least 3 rollers.
Standard widths: 470 mm, 570 mm, 670 mm
Design height
100 mm
Surface finish
Zinc plated
Skate wheel rail table
Frame structure
Steel C-profile, galvanised, with bolted cross braces
Frame dimensions: 100 mm x 30 mm x 2 mm
The rails with the skate wheels are bolted or welded onto the steel cross braces.
Conveying elements
Conveyor skate wheel rail RLU33
Conveyor width
The width is determined by the properties and weight of the unit load – the unit load should be resting on at least 3 rollers.
Standard widths: 320 mm, 470 mm, 620 mm
Design height
100 mm
Surface finish
Zinc plated
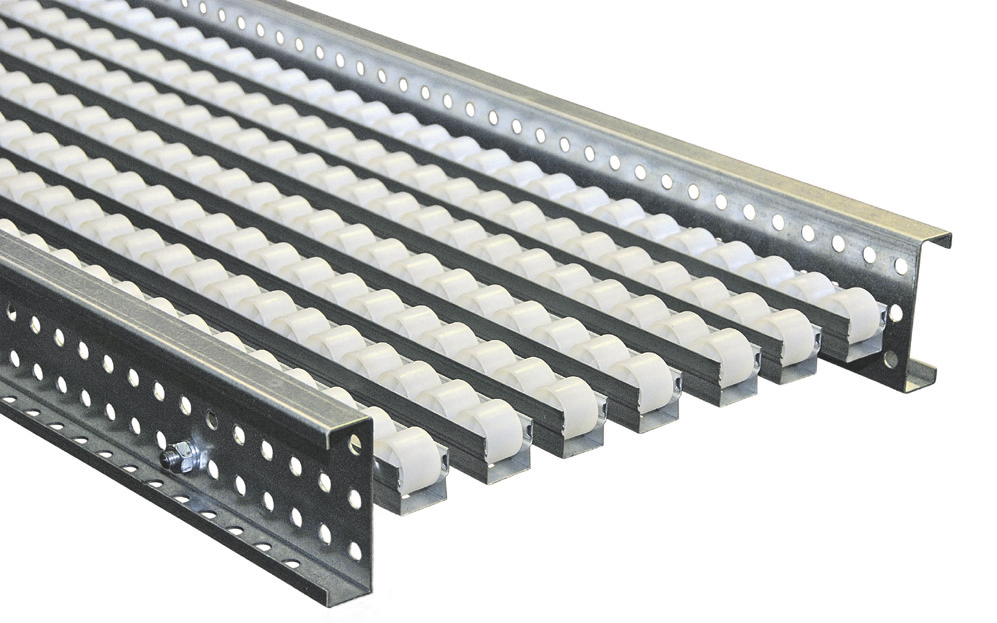
All-side rollers and rails, conveyor skate wheels
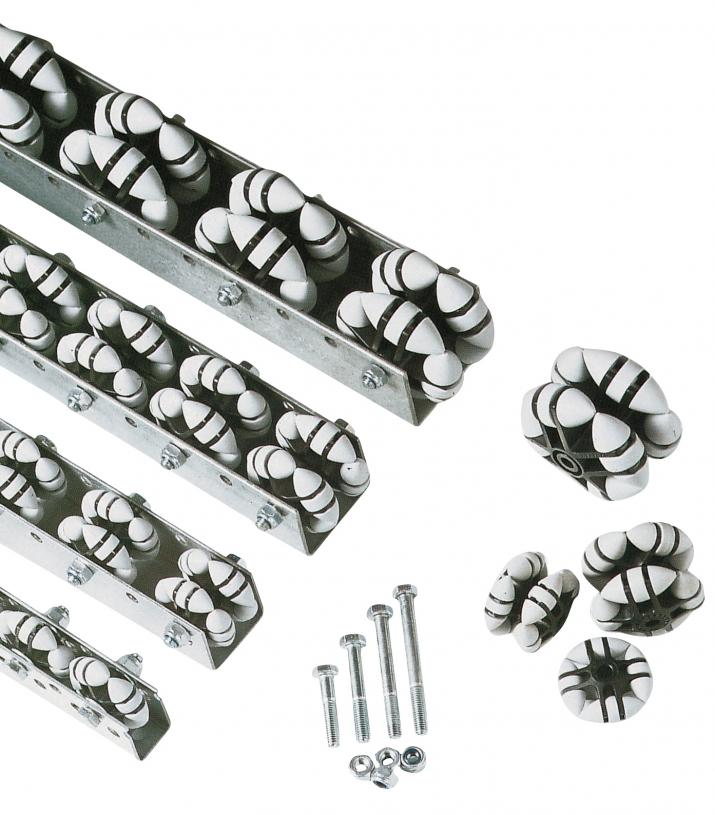
All-side rollers and rails
Use
Conveyance of unit loads at right angle to the main direction of movement
Technical execution
All-side rollers are made of a galvanised steel profile. The profile is fitted with all-side rollers in certain spacings. Two rows of holes on the rail base are used for fastening the rail to the sub-structure.
Spacing pattern of the rows of holes: 33.3 mm | hole diameter: 8.1 mm
Advantages
Every roller can be exchanged individually
Creation of any size of table area possible
Steel axles guarantee high load capacity and low sliding friction resistance
Conveyor skate wheels
Technical execution
Material plastic or steel
Mounting in two rows (plastic skate wheels)
Use
As a component part of skate wheel conveyors, picking shelves etc.
Advantages
Simple
Low cost
For versatile use
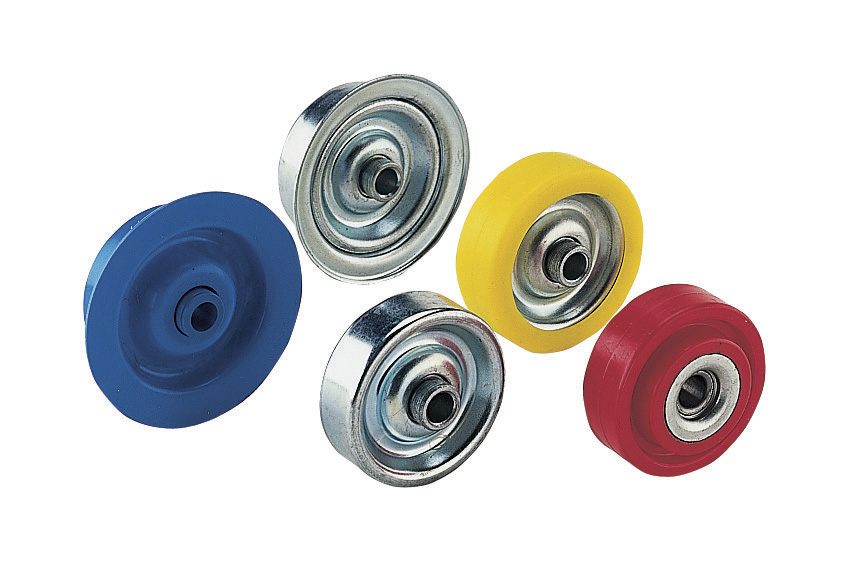
Skate wheel rails
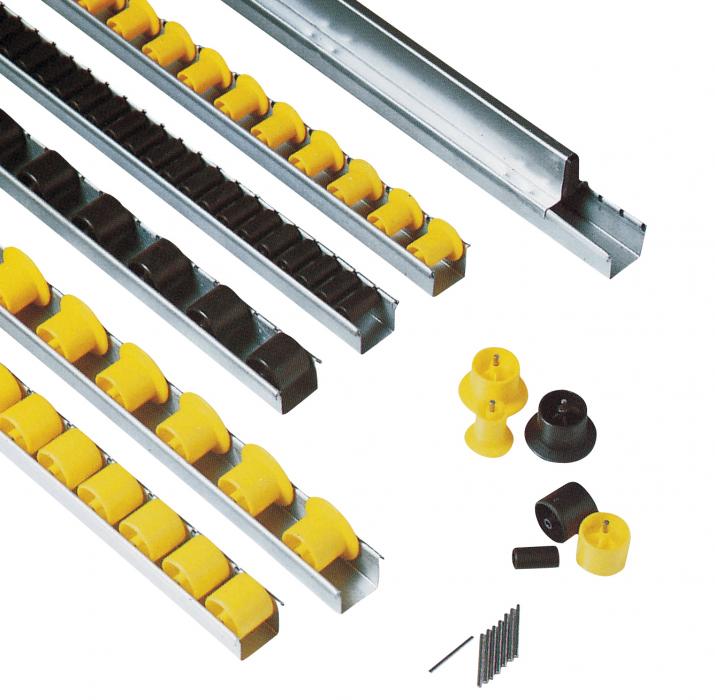
Technical execution
Carrier profile made of galvanised sheet steel or stainless steel
The skate wheels are mounted on steel axles
Skate wheels made of high-quality thermoplastic material
Use
Main field of use: in flow racks
As guide rails in conveying systems
As skate wheel conveyors to link working stations
As picking tables
Advantages
Safe running
Mounting on steel axles guarantees a high load capacity and low sliding friction resistance
Simple assembly
With standard skate wheels, flanged skate wheels, skate wheels made of thermoplastic material
Impact-resistant and break-proof, resistant to acids and alkalis, no humidity absorption
Universal wheel rails
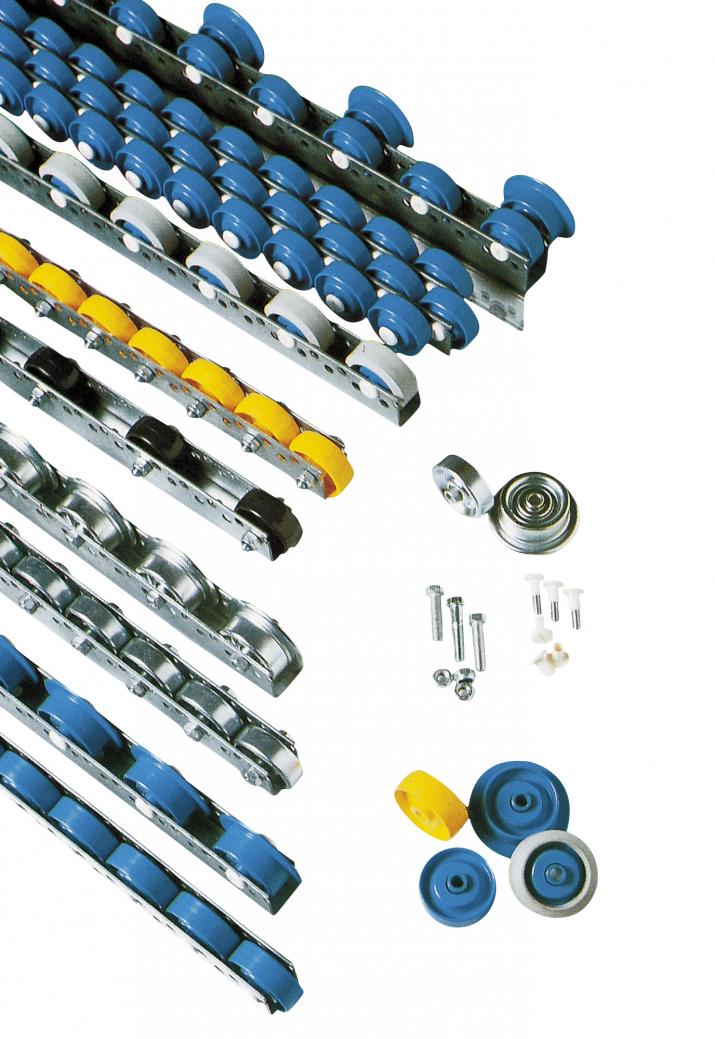
Technical execution
Universal wheel rails are made up of a galvanised steel profile with two rows of holes at different heights at the side and one row of holes in the rail base.
Spacing pattern of the rows of holes: 25 mm | hole diameter: 8.1 mm
The rail design makes it possible to fix customary Ø 48 mm skate wheels using special screws, hollow rivets or M8 screws in a 50 mm, 75 mm, 100 mm etc. grid pattern. Several skate wheels can be fixed next to one another in one or several rails. The skate wheels can be combined offset to one another and in different versions. Unless ordered otherwise separately, standard skate wheels are fixed in the lower row of holes, flanged skate wheels in the upper row of holes.
Use
Flow racks
Guide rails, side deflectors and carrier rails in conveying systems
Roller conveyors for linking two working stations
Packaging machines
Advantages
Mounting of the skate wheels on steel axles guarantees a high load capacity and low sliding friction resistance
Can easily be integrated in existing systems
Space-saving use
Optimum adaptation to the load capacity actually required
Sturdy design
Maintenance-free ball bearings with long service life
Flow racks
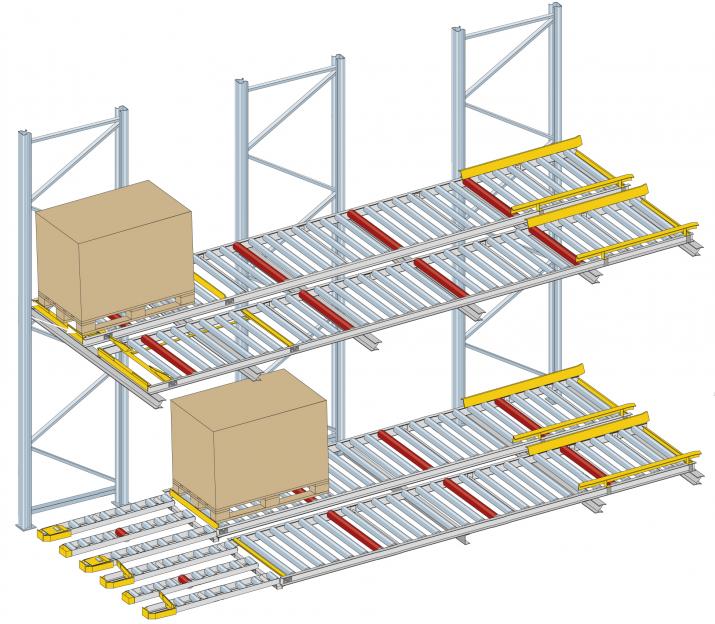
Technical execution
Flow racks are made up of a support frame system and flow levels. The support frame system bears the flow levels and is dimensioned in relation to load and size depending on operating requirements: The flow levels are integrated in the support frame system and adjustable in height and angle. Their design (number of channels, flow depth, load and properties of the running surface of the load carriers used) depends on the material to be conveyed.
Versions
Light load flow level
Combined flow level
Heavy load flow level
Advantages
Optimum use of existing storage capacities: Up to 30% space can be saved by doing without superfluous aisles.
Time saving: Travel time savings of between 40% and 70% are achieved during picking.
Clear provision of the goods for fast removal.
First-in/first-out principle is prescribed by flow rack storage: no re-storage, simple monitoring of best-by dates etc.
Cost saving lower space requirement, power-less automation, no special transport vehicles required, lower personnel expenditure
Rollers instead of shelves (plastic rollers in two colours)
Can be extended at any time
Very high load capacity