Affordable cutting edge technology with highest reliability!
Only ONE drive roller fits for all velocities of conveying
- Free wheeling, automatically holding position
- Deceleration behaviour
- Highest plant availability
- Longest life time
- Lowest current consumption at given conveying task: optimized power supply and wiring
- Very low noise level: < 50 dB
- Maintenance free, no wear parts, most sustainable bearings
- Electrical and mechanical design induces highest reliability and energy efficieny
- Contact free conveying via logic functions
FIELDS OF OPERATION: Roller conveyors | Belt converyors | Lifting platform loading | Packaging | Layer handling | Scales loading | Lifting units | Washer loading
BRANCHE: Automotive Industry | Food Industry | Mechanical Engineering | Measurement Technology | Packaging Technology | Warehouse Logistics | Production Logistics | Pharma
Products
Performance
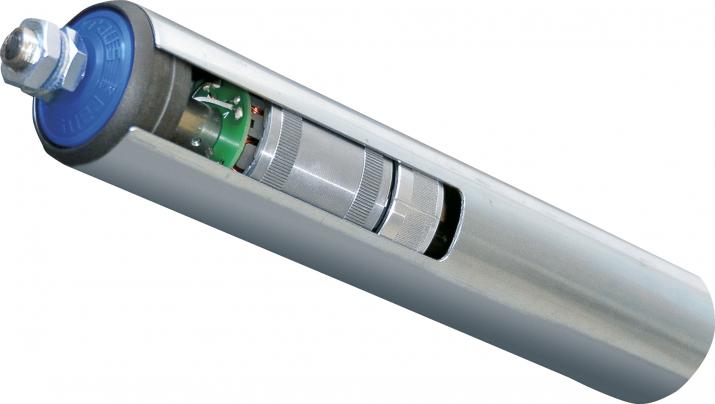
Conveying speeds
continuously selectable up to 2 m/s
Mass conveyed
up to 100 kg per drive roller
Supply voltages
24 V and 48 V
Operating modes
S1, S3, acceleration, deceleration, magnetic holding torque, freewheeling (no gear box)
Speed control
analogue and digital
Protection
short circuit, over current, over voltage
Rated ambient temperature
0 °C to 40 °C (others on request)
Degrees of protection
IP 54, IP 20
Drives
round-, timing-, chain- and flat-belts, chains, without drive head for direct drives and conveyor belts
Motor controller
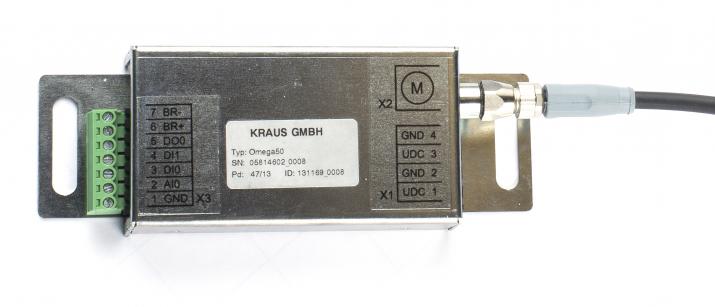
The motor controllers include the drive control system and the control logic. The DC voltage is converted into a three-phase current according to the control Signal.
The motor controller includes a brake chopper to derive surplus energy to a resistor. The mind is the sensorless control of the polar wheel angle which provides the full force at any time.
Motor controller MCP
The controller MCP offers analog and digital modes of the speed control.
Motor controller MCL
The controller MCL provides additionally logic functions and accumulation conveying with zero pressure: Single release mode and block release mode. A gap between the goods is kept at any time.
The MCL has two interfaces for sensors. Thereby e.g. specific start and stop of one sector can be implemented without additional control efforts.
Logic and perfomance
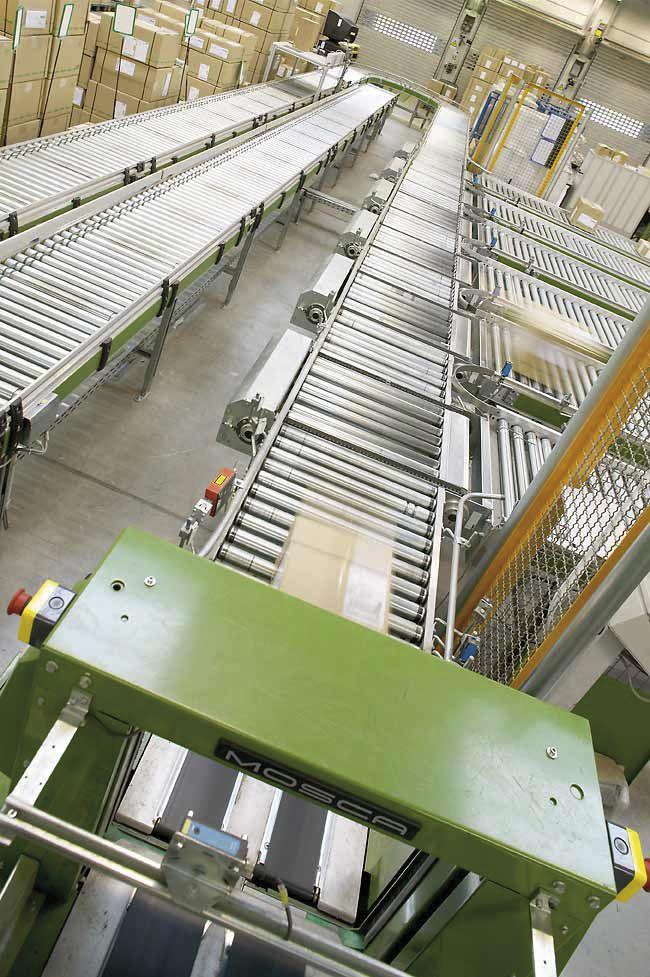
Logic Functions for highest flow rate
A segment consists of a drive roller, driven rollers, a motor controller and a sensor. The logic functions are either integrated in the motor controller MCL or sensors integrate them. Thereby the good in the specified segments of a conveyor line are automatically started and stopped.
Advantages
No need for central processing of the signals of each segment (start/ stop and empty / occupied)
Touchless flow of goods on conveyers without an additional programming effort
Easy wiring and low installation expenses
Singularising Intake Mode
The conveyed good runs through the complete line and get stopped at the last segment LCn. So the segment LCn is occupied. The LogiCARD control stops the next conveyed good contactless at LCn-1 as long as the following sector LCn is occupied. This information passes the LCn to LCn-1, i. e. the next good get stopped by LCn-1 in the respective Segment.
Singularising Release Mode
With singularising release mode the good LCn-1 proceeds if the good LCn has left it's segment completely. This information passes each LCn to the upstream LCn-1. In turn the LCn-1 starts it's upstream segment - and so on. Through this the goods are transported one by one from a segment to the following.
Block Intake Mode
The LogiCARD stops the promoting goods are touchless (in the block) in the buffer area and stay there till release signal from LCn arrives. A block of coveyed goods passes through the complete sector and get stopped at the last LCn of the sector. A block covers at least two successive segments, however, don't lead to the stop of the individual segments or don't let any gaps between promoting goods arise on the way to the last Segment. Occupied are now the segments LCn till LCn-length of block. The LCn passes this information to the LCn-1. That means the following good is recognized and stopped in the segment n-1 by the LCn-1. The goods aren't shoved together within a block and remain touchless.
Block Release mode
With the block release mode all goods at a block of segments get moved, if the following zone is free. Usually all segments are passing once the last segment is empty; where applicable the whole downstream block has to be empty before. To increase the flow rate all segments of one removing block are started nearly at the same time.